Introduction: Classroom-Ready Modular Cymatics Experiments Rig
This modular setup is the result of a several-years-long quest to improve cymatics experiments for use in elementary school music class.
I am an elementary school music teacher (K-5) in Nashville, Tennessee, and my ever-changing "science of sound" unit is always one of my favorites to teach. The unit culminates with "experiment day", when I get to take my students with me down the infinitely fascinating rabbit hole that is cymatics experiments.
In short, cymatics is the study of sound made visible: audio frequencies are used to affect physical matter.
The idea behind incorporating cymatics experiments in music classes is to help students understand the relationship between sound and physical matter. With this modular setup, students can now witness the effects of sound waves on different materials, such as sand, water, and even metal plates. Cymatics experiments give students the opportunity to explore the science behind music and providea fun and engaging way for students to learn and understand the principles of sound.
However, demonstrating some of these experiments in an elementary school classroom presents several unique challenges. First, time: my 'science of sound' lessons are necessarily fast-paced and action-packed; when we get to the experiment portion I need to have things set up to demonstrate back-to-back before the end of the 45 minute class. Some cymatics experiments are easy to pull off: making patterns with sand on a balloon, violin bow on a metal plate, even my acoustic levitator; the Chladni plate (sand makes patterns on a vibrating metal plate) and "water in speaker" experiments not so much.
Why it hasn't worked:
- Way too loud - especially the Chladni plate experiment
- Requires several cables - setup is too involved and takes too long
- Too big - requires more than one trip to transport across the room
- Too much 'calibrating' - Requires fiddling with things for a bit until it works (leveling the plate, etc.)
- It is difficult to juggle amp volume and tone frequency when one requires a touchscreen or buttons (or anything that isn't a knob)
- Using hacked-up amps makes me nervous around water and keeps everything tethered to a wall outlet
To circumvent these challenges, my goal was to create the smallest, simplest possible electronic device to demonstrate multiple easily-reproducible cymatics experiments in my elementary school music classroom.
This device will be constructed as 4 modules, in this order: the tone generator module (which operates the others), the Chladni module (used with plate or upside down), the waterproof speaker module (of which I made 4 different sizes), and the balloon attachment (to be used with any of the speakers). All of the 3d-printed parts were designed in Tinkercad, and links to the files and projects are provided per step.
Supplies
Tone Generator Module Materials
- WSFG-06 Tone Generator Module
- Lm386 Audio Amplifier Module
- 9v + holder
- SPST switch
- 1k potentiometer
- flexible stereo aux cable
- Soldering iron / solder / wire
- Magnets (1.2”)
- UV resin and UV lamp
- M3 bolts
- Component brace
- 4x Screw posts
- Knobs (dB and Hz)
- Cable winder
- Winder handle side/magnet side
- resin mold for bottom
Chladni Module Materials
- Resonance speaker
- ⅛” jack
- Fine grain sand/salt shaker
- Metal plate (I made three- one repurposed from a broken mixer, a 18"x6" (16 guage) piece of metal from Home Depot, and a Chladni plate available on Amazon)
- 5mm LED
- 1k resistor
- M3 bolts
- UV resin and UV lamp
- enclosure
- speaker brace
- 4x spacers
- resin mold for bottom
Waterproof Speaker Module Materials
- Speaker (4Ω-32Ω impedance)
- Waterproof spray
- ⅛” jack
- 5mm LED
- 1k resistor
- UV resin and UV lamp
3d prints:
Balloon Attachment Module Materials
- large balloon (36" worked for me)
- rubber band
3d prints:
Step 1: TONE GEN MODULE: Prep
The WSFG-06 Tone Generator Module will generate the sine wave for our experiments. The button labeled 'P3' will put it into sine wave mode.
Super glue magnets onto component brace and winder magnet mount.
Use double-sided tape to adhere the LM386 module to the bottom of the tone generator.
Super glue screw posts at each corner of the bottom of the tone generator.
Tinkercad project with 3d prints
All of the STL files for the Tone Gen 3d prints are attached to this step.
Attachments
Step 2: Wire Tone Generator to LM386 Amp
Solder wires to the four pins on the end of the LM386 and connect them to the tone generator as shown in the image.
Step 3: Assemble the Retractable Cable
Feed the TRS cable into the component bracket. Cut the plug off of one end of the cable and strip the cable to expose the 3 wires inside. Identify which is the tip/ring/sleeve. Strip the 3 wires and solder a wire to each.
Solder the wires from the TRS cable to the switch and pot as shown in the image.
Step 4: Finish Wiring Switch and Volume Pot
Connect wires to the "OUT" and "GND" screw posts on the LM386, then solder them to the volume pot as shown in the image (OUT to lug 3, GND to lug 1).
Connect two wires to the switch; one will go to the LM386 VCC, the other will go to the battery +
Step 5: Assemble Enclosure; Finish Wiring
Super glue the component brace under the lip of the tone generator. Hot glue the 9v holder next to the component brace, making sure that the leads to the battery are still exposed.
Solder the wire from the middle lug of the switch to the battery +, and the wire from the bottom lug of the switch to the LM386 VCC. Connect the battery - to GND on the LM386.
See the image for full wiring scheme.
Step 6: Create Resin Bottom Panel
UV resin is an incredibly handy medium! I like to make enclosure panels this way because it's WAY faster than printing something as solid. Additionally, the molds can be printed to the exact shape you need, saving you the chore of cutting plexiglass.
To use UV resin: 1. Pour in the sauce. 2. Blast it with the light!
Place the resin mold on a sheet of plexiglass (no need to hold it down- if some creeps out from under, it's easily cut away once cured)
Pour in resin, blast it with the light for a few minutes. A UV nail lamp works great for this. You'll know it's fully cured when the panel snaps easily off of the plexiglass.
Step 7: Drill and Attach Bottom Panel
Mark the bottom panel at the screw posts and drill.
TIP for drilling resin without cracking:
Keep in mind that if you try to drill a hole straight through, the resin will likely crack. Instead, you’re trying to displace material little by little- drill for about one second until shavings come out, then clear the shavings and blow off the end of the drill, and repeat all the way through.
Step 8: Assemble Winder; Attach Knobs
Assemble the cable winder as shown in the image. Tone generator module done!
Next, the Chladni module...
Step 9: CHLADNI MODULE: Place Speaker and Install Jack
Place speaker.
Install jack.
Tinkercad project for 3d prints
All of the STL files for the Chladni Module 3d prints are attached to this step.
Step 10: Wire LED
Wire the LED to the jack and speaker as shown in the image.
Step 11: Create Bottom Panel; Finish Enclosure
Just like with the tone generator bottom panel:
1. Pour in the sauce. 2. Blast it with the light!
The 3d-printed mold can be cut off once cured to allow the LED to shine through.
Mark and drill the panel at the screw posts, attach bottom panel.
Attach the speaker brace with the spacers and M3 bolts as shown in the image.
Step 12: Prepare Plate
Mark the center of your metal plate and drill.
Use an M5-.8 bolt (or whatever fits into your speaker) and attach the plate with as many nuts as will leave about 3mm of threads exposed. A 10mm bolt with 2 nuts was perfect for me.
Pictured are a metal plate repurposed from a broken mixer, a 18"x6" (16 guage) piece of metal from Home Depot, and a Chladni plate available on Amazon
Chladni module complete!
Next, the waterproof speaker...
Step 13: WATERPROOF SPEAKER MODULE: Prepare LED
I made four of these with speakers of different sizes: 2", 3.5", 4.5", and 6". Attached are files to 3d print each of the enclosures, and their respective tinkercad projects are linked below.
To make the 'water in speaker' experiment more effective, we'll put an LED inside the speaker beneath the water by enclosing it completely in resin.
-solder 1k resistor to short leg of LED
-solder a wire to the long leg of the LED, and another to the other side of the resistor
Enclose in resin and cure. I used a small mold meant for chocolate (I think?) but the corner of a clear plastic bag would also work.
Test to make sure the resin is watertight: light the LED by touching the ends of the wires to either side of a 9v battery. Then, submerge the LED in water- if it stays lit, you're good!
Tinkercad projects for enclosures:
All of the STL files for the Waterproof Speaker Module 3d prints are attached to this step.
Attachments
Step 14: Install LED; Spray
Feed the LED wires into the speaker, and press the LED gently onto the dust cap of the speaker.
With the LED pushed down, hot glue to secure it in place
Spray on a couple coats of the waterproof sealant and let dry
Step 15: Wire LED to Speaker and Jack
Install jack in enclosure, and solder to speaker and LED as shown in the image (wiring scheme is the same as the Chladni module)
Step 16: Seal It Up!
Seal up any gaps where water might get through. Hot glue and plastic bags work well, just be careful not to get glue on the speaker cone.
Step 17: BALLOON ATTACHMENT: Attach Balloon
Cut off the part of the balloon that you blow into, then cut a slit so that the balloon can be laid flat over the printed attachment
Stretch balloon evenly over attachment and secure with a rubber band.
Tinkercad projects for prints:
Step 18: EXPERIMENT TIME!
Tone generator:
The tone generator module is the brains of the operation, it sends the tone to whichever module is connect via the retractable TRS cable. The button labeled 'P3' on the tone generator will put it into sine wave mode.
Chladni module:
Screw the plate onto the Chladni module speaker and sprinkle some sand evenly across the plate. Fire up the tone generator and see what happens!
Can also be used upside down! Try placing it upside down on a large drum, add sand and watch the patterns. The patterns will change as the speaker is moved around on the drum.
Waterproof speaker module:
Just add water!
Balloon attachment:
Simply set on top of one of the waterproof speaker modules and sprinkle some sand onto the balloon. Fire up the tone generator and watch the sand move!
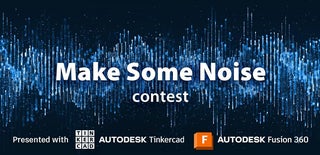
Participated in the
Make Some Noise Contest